Laundry Tracking
RFID Laundry tracking is a modern solution designed to streamline and optimize the operations of laundry businesses. It is a system that uses technology, often Radio Frequency Identification (RFID), to monitor, count, sort, and manage laundry items. The purpose of laundry tracking is to eliminate manual errors, improve efficiency, and provide real-time inventory management. This is particularly important in businesses where large quantities of linen need to be washed each day, such as hotels, hospitals, and large-scale laundromats.

The benefits of using a laundry tracking system are manifold.
Firstly, it significantly improves efficiency by automating the process of counting and sorting soiled and clean linen. This not only saves time but also reduces the manpower required for these tasks.
Secondly, it reduces the chances of loss or misplacement of items, as each piece of linen is tracked individually. This can result in substantial cost savings in the long run.
Lastly, it provides better inventory management by keeping track of the number of washes each linen item has gone through, thus enabling businesses to plan for replacements in a timely manner.
RFID Laundry Tags
In a typical laundry business setting, the laundry tracking system works by attaching RFID tags to each linen item. Each laundry item, such as a towel or bedsheet, is tagged with an RFID tag. These tags are then read by RFID readers, which can be tagged and tracked, enabling accurate counts, sorting of soiled and clean linen, and even tracking the location of each item. The system can also record the number of washes each item has undergone, providing real-time inventory management.
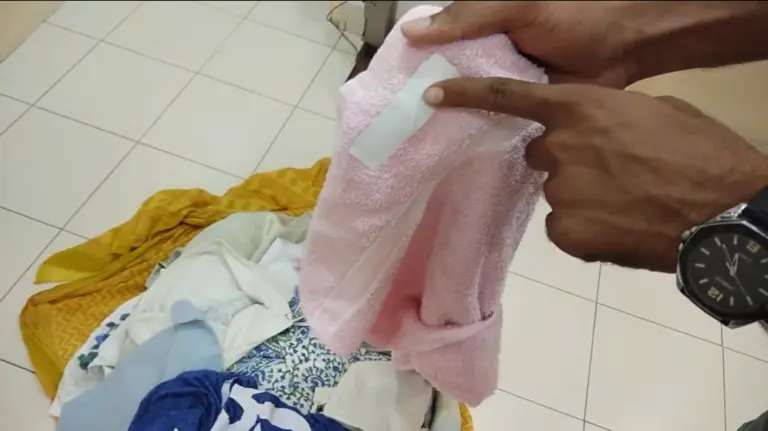

RFID Laundry Tags are either sewn or heat-sealed. These tags are designed to withstand the harsh conditions of the laundry process, including high temperatures and exposure to water and detergents.
Key Features of Laundry Tracking System
Time-saving: The system automates the counting and sorting process, saving valuable time.
Reduction in lost items: By tracking each piece of linen, the chances of losing items are significantly reduced.
Inventory Management: Count your washed and soiled linen in seconds, reducing the risk of errors associated with manual counting. The system also segregates and tracks the location of each linen item, providing real-time updates on your inventory.
Automated Notifications: Receive alerts when a specific linen item has reached its maximum number of washes, helping you maintain the quality of your linen and prevent overuse.
These benefits can be particularly advantageous for businesses such as hotels or hospitals, where managing large quantities of linen on a daily basis is a necessity.